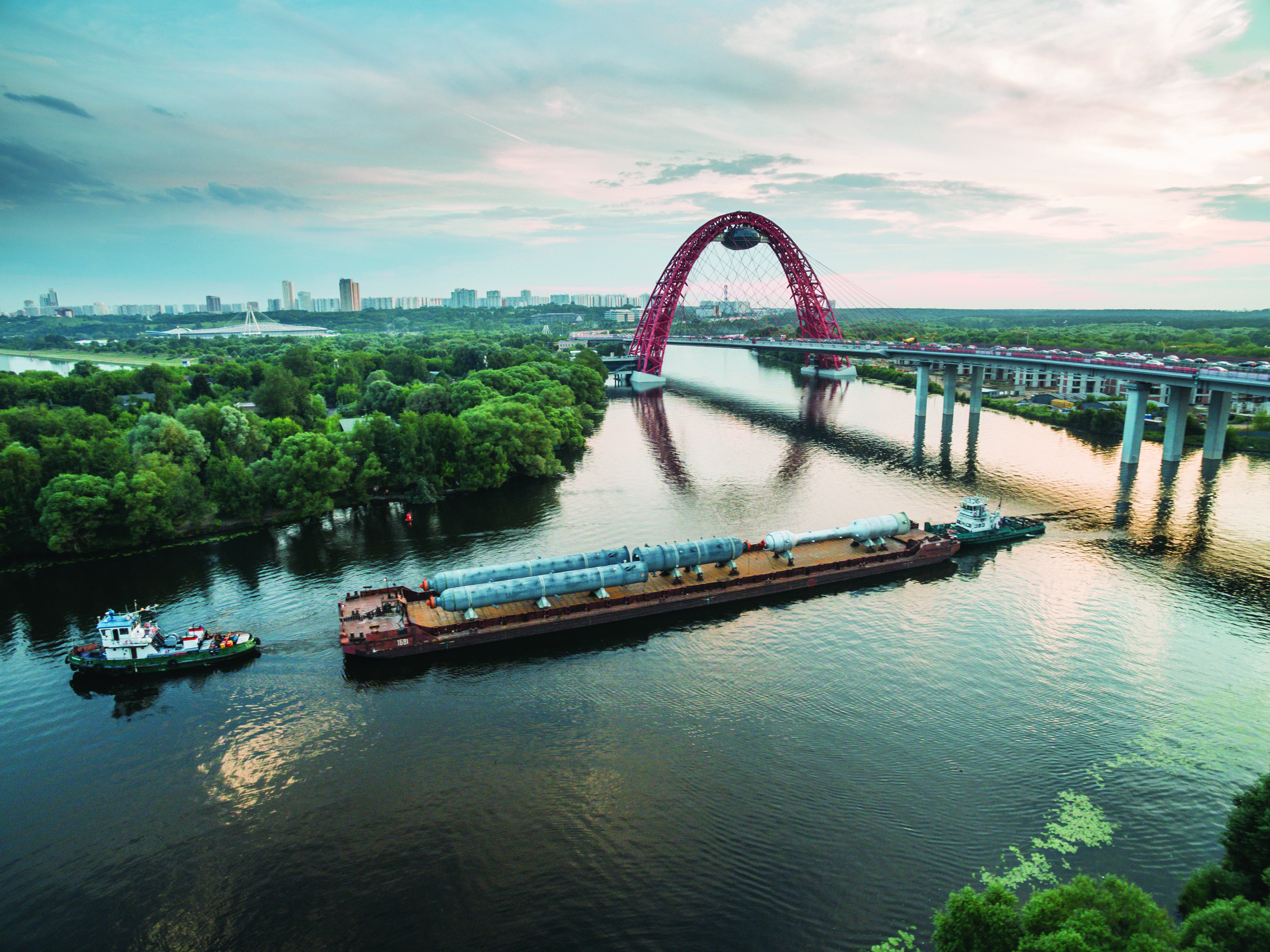
Nel febbraio 2018 Maire Tecnimont si aggiudica la progettazione e la realizzazione di una colonna lunga 54 metri da installare in Siberia. Ecco come è andata.
A metà agosto Omsk, settima città della Russia situata sul fiume Irtysh, non lontana dalla frontiera col Kazakistan, è stata teatro di un trasporto di grande rilevanza per il gruppo Maire Tecnimont. Qui si è concluso il viaggio di una colonna per il trattamento degli oli derivati da idrocarburi, realizzata in d’acciaio, pesante più di 100 tonnellate e lunga 54 metri.
La straordinaria e complessa operazione, avviata il 10 luglio a Brindisi e conclusa quaranta giorni dopo nel cuore della Siberia, si è interamente svolta senza fare ricorso a strade o ferrovie. Lunga quanto un palazzo di 15 piani e interamente costruita in acciaio al carbonio, la torre ha viaggiato lungo le acque di mari e fiumi per migliaia di chilometri, trasportata su mercantili da navigazione oceanica e chiatte fluviali specifiche per i contesti siberiani.
Un trasporto eccezionale
La colonna per il trattamento degli oli derivati da idrocarburi è destinata alla raffineria di Omsk, una fra le più tecnologiche della Federazione Russa e tra le più grandi al mondo, con una capacità complessiva di trattamento del greggio di circa 21,3 tonnellate all’anno. Spiega Enrico Rolandelli, responsabile Ingegneria e Operation di Tecnimont:
“Da febbraio 2018 con il cliente GazpromNeft abbiamo un contratto EP+Cm per costruire una nuova unità Delayed Coking all’interno della raffineria: la struttura servirà a espandere la capacità di conversione di residui pesanti, ottimizzare la produzione di distillati, ridurre l’impatto ambientale e produrre coke di grado anodico che contribuisce a modernizzare la raffineria per la produzione di carburanti Euro5. Grazie a questa commessa, oltre a rafforzare una collaborazione strategica con un cliente importante, consolidiamo la nostra presenza in Russia come fornitori affidabili di servizi ad alto valore aggiunto per il mercato locale”.
Da Brindisi a Omsk in 40 giorni
Gli otto elementi che componevano il trasporto speciale sono stati prodotti da aziende italiane qualificate, con sedi tecniche a Cremona e Treviso, e stabilimenti produttivi a Brindisi e Vibo Valentia. Sette blocchi - quelli più “piccoli” - misuravano tra i 20 e i 38 metri di lunghezza, mentre la già citata torre - composta da due pezzi assemblati - superava da sola i 50 metri.
Per trasportarla dalla fabbrica alla nave è stato utilizzato un carrello speciale, elettronicamente comandato, che viaggiando a passo d’uomo in una notte ha percorso i tre chilometri fino al porto di Vibo Marina. Dopodiché il carico speciale ha viaggiato via mare fino a Brindisi, per caricare gli altri elementi e partire definitivamente alla volta della Russia.
“Ripercorrere le varie tappe - spiega Enrico Santi, Direttore di Progetto Tecnimont per la commessa di Omsk - è utile per capire la complessità delle situazioni da gestire e l’alto livello di preparazione dell’intera catena progettuale e operativa. Partito il 10 di luglio dalla Puglia, il convoglio ha percorso oltre quattromila chilometri: dal Mediterraneo ha transitato per Gibilterra, circumnavigando l’Europa e costeggiando Danimarca e Norvegia nelle acque del mare del Nord. Al porto russo di Sabetta (nella penisola di Yamal, al circolo polare Artico) la colonna è giunta venti giorni dopo, per poi approdare il 3 agosto a Novy Port, dove è avvenuto il passaggio dalle navi oceaniche alle cosiddette ‘barges’, le chiatte in grado di navigare i fiumi della Russia. Uno snodo di grandissima precisione, basato su analisi fatte per ottimizzare al meglio le delicate fasi di scarico e carico degli elementi”.
Arrivare puntuali a Sabetta e a Novy Port era altrettanto strategico: la finestra del disgelo lungo i fiumi Ob e Irtysh dura solo una sessantina di giorni l’anno, da metà luglio a metà settembre. Sbagliare una decisione e commettere anche un singolo errore poteva significare dodici mesi di ritardo sul progetto, con un incredibile ventaglio di costi e penali da pagare. Riprende il project director: “Ogni ingegnere sa bene che le analisi e le pianificazioni sono fondamentali per ridurre i rischi al minimo, ma non per annullarli completamente. In fase di brain storming, immaginare il maggior numero possibile di implicazioni ci ha permesso di gestire ogni variabile di percorso. Questa volta l’imprevisto è apparso sotto forma di nebbia, che ha costretto il trasportatore a fermare le chiatte per tre notti, evitando danni e complicazioni ben peggiori”.
Il 20 agosto, dopo poco più di due settimane, il convoglio è finalmente giunto al molo della dogana di Omsk, dove è rimasto fermo alcuni giorni a causa delle numerose procedure burocratiche previste. “Prima di scaricare qualsiasi elemento - continua Santi - occorre verificare che i materiali corrispondano alla montagna di carte documentali allegate al trasporto. Un lavoro di grandissima attenzione, specialmente in Russia, dove la flessibilità e il sangue freddo fanno la differenza. In questo caso il minuscolo imprevisto aveva le dimensioni di un foglio A4, un documento a cui mancava un timbro di certificazione. Fortunatamente, non lo dico per esagerazione, gli ingeneri italiani sono i numeri uno quando si tratta di lavorare in emergenza h24. Grazie a una giusta dose di reattività creativa, in 72 ore abbiamo rielaborato una nuova procedura che ci ha permesso di passare la dogana”.
Lo sbarco siberiano
L’ultima casella del percorso era lo scarico con gru di precisione e il trasbordo delle colonne, dalle chiatte ai carrelli motorizzati multi-ruote. Su questi mezzi, il carico è arrivato in fondazione dopo quattro chilometri di strade di cantiere. “Le ultime micro-decisioni fondamentali sono state quelle prese per agevolare il trasporto dei pezzi, nel tragitto dal molo all’impianto GazpromNeft. Far passare un elemento d’acciaio lungo 54 metri senza ostacoli implica uno studio accurato per calcolare le pendenze minime, il raggio delle curve, la larghezza e la tenuta dei ponticelli. Abbiamo rinforzato e allargato passaggi, asfaltato tratti sterrati, eliminato semafori e alzato cavi elettrici. Dopo tutto questo viaggio, sbagliare l’ultima decisione sarebbe stata una beffa incredibile. Il successo dell’operazione è vedere il cliente che in una manciata di minuti accerta che tutto si è svolto nei tempi e nei modi previsti, in qualità e in sicurezza. Solo noi, dopo un impegno di dodici mesi - dal progetto alla consegna e installazione- sappiamo tutto quello che c’è dietro. E quando il lavoro finisce, la soddisfazione corre dalla Siberia a Milano, alla velocità della luce!”.
La missione si è concretamente conclusa a fine settembre, grazie alla perizia del team che ha installato la colonna in fondazione in tutta sicurezza. GazpromNeft e Maire Tecnimont hanno aggiunto un altro tassello di una storia di reciproca collaborazione. Dai trenta gradi di Puglia e Calabria, fino all’autunno nel cuore della Russia: la torre d’acciaio non teme sbalzi termici e ora svetta sull’impianto di Omsk. Per la curiosità dei viaggiatori della Transiberiana.
La scelta del percorso
Gli studi fatti negli anni e le competenze evolute in materia di logistica hanno consentito di prendere decisioni strategiche di grande importanza, optando per un piano di trasporto navale in grado di gestire elementi di grandi dimensioni (difficilmente transitabili per via terrestre o ferroviaria). “C’era tutto un tema di soggetti da coinvolgere lungo il tragitto - afferma Rolandelli - di documentazione ad hoc da preparare, di scenari e proiezioni di rischio da disegnare. Tra l’altro un paio di anni fa, quando è partita la commessa, il cliente GazpromNeft aveva manifestato il proposito di far arrivare i materiali a Omsk utilizzando tracciati diversi da quelli abituali. La loro idea era di percorrere la rotta dell’Artico, che collega la Norvegia alla Cina, grazie all’entrata in funzione di nuove navi rompighiaccio a propulsione nucleare, con motori da 350 megawatt in grado di sfondare lastre spesse tre metri”.
Scegliendo la rotta marittima settentrionale (la cosiddetta ‘Via polare della seta’ che consente a una nave di viaggiare da Shangai a Rotterdam in 33 giorni, invece che passare da Suez e mettercene 50), il progetto avrebbe avuto caratteristiche completamente diverse. “L’obiettivo iniziale di GazpromNeft era di coinvolgere fornitori cinesi e utilizzare questa nuova via: ma un ritardo nell’inaugurazione della Polar Silk Route ha creato una situazione di stallo. Da parte nostra, conoscendo le tematiche logistiche interne alla Russia, abbiamo preferito riproporre rotte e piattaforme già sperimentate in occasione di altri impianti realizzati a Omsk, l’ultimo dei quali è stato avviato cinque anni fa. E così, alla firma del contratto abbiamo preso una serie di decisioni, convinti che le nostre scelte fossero funzionali alla qualità migliore e ai parametri del progetto: insieme alle analisi su costi, rischi e tempistiche, abbiamo caldeggiato l’eccellenza della nostra catena di fornitori europei, nel caso specifico per la maggior parte italiani, che garantiscono performance elevate e stabili nel tempo, anche a temperature polari come quelle di Omsk. Di fatto l’accountability e la leadership acquisita, insieme a un quadro dei costi adeguato ai loro obiettivi, hanno portato i risultati previsti: il convoglio con la colonna d’acciaio è arrivata puntuale alla penisola di Jamal, proprio nella finestra temporale tra l’inizio del disgelo e la piena del fiume. E successivamente, fino alla raffineria di Omsk”.
Le fasi del progetto: dall’ideazione all’installazione, passando per la realizzazione
Un’esecuzione tutt’altro che banale, vista la rotta praticata, i rischi potenziali e le casistiche di trasporto da rispettare. A questo si aggiunge una burocrazia documentale non semplice da predisporre e codificata secondo un iter di autorizzazioni e passaporti anche per le merci. “Ci siamo preparati con grande impegno, tempi adeguati e figure professionali specifiche”. “Tutto parte da due fasi: lo studio creativo e la redazione del piano esecutivo di progetto, il cosiddetto ‘Project Execution Plan’. Nel nostro mestiere - e questo vale per ogni commessa - sia le attività operative che le possibilità di raggiungere l’obiettivo dipendono dalla qualità di questi due step iniziali. Più disponi di fantasia, esperienza e creatività per capire dove devi arrivare, e come ci devi arrivare, meno problemi futuri avrai lungo il percorso.
Il primo l’abbiamo ribattezzato ‘pensatoio’, in inglese è il tipico brain storming, dove si analizzano tutte le variabili e le criticità che si possono incontrare; il secondo è la messa su carta delle migliori idee emerse, in sequenza esecutiva. Intorno a quel tavolo, è il caso di ribadirlo, ogni decisione conta. Il leader di progetto, conoscendo il contratto e l’obiettivo, chiama a raccolta i referenti della logistica, del procurement, del trasporto e della costruzione per raccogliere e scambiare il maggior numero di pareri possibili sulle diverse attività. Il confronto di esperienze e le singole diversità aiutano a scomporre le implicazioni passaggio per passaggio, iniziando così a definire un quadro più compatto e pulito”.
In uscita da queste due fasi, il project control manager stabilisce le sequenze e le tempistiche entro le quali gli eventi devono avvenire. Da qui - dopo lo studio creativo e il piano esecutivo - si passa alla terza fase, quella della progettazione tecnica guidata dal project engineering manager.Una figura a metà tra l’ingegnere e il manager, con vaste competenze su entrambi i fronti e una grande capacità di leadership per coordinare, supervisionare ed effettuare il controllo complessivo dei lavori.
Continua Santi: “Oltre a definire la meccanica di processo, le fasi operative, i collaudi e i controlli, la commessa ha bisogno dell’apporto del project procurement manager, che deve selezionare i fornitori, condurre le trattative commerciali e pianificare gli acquisti dal punto di vista operativo. Com’è facile immaginare, ogni decisione anche minima va a incidere profondamente sul progetto: sbagliare o non aggiornare la qualifica di un fornitore (ovvero valutarne in modo errato la stabilità finanziaria, la capacità produttiva o le certificazioni di qualità) può significare un grave ritardo sui tempi e un conseguente aumento dei costi. Questo lavoro organizzativo parte da un principio di base: quello della sicurezza di tutte le persone coinvolte nel lavoro di dettaglio. Per questo la preparazione del piano di safety ha coinvolto tutto il team che ha partecipato a questa impresa. Per noi gestire situazioni complesse in condizioni di incertezza è all’ordine del giorno”.
L’attività di Post-Order, intesa come ramo del Procurement, si scompone nella quality inspection (con l’obiettivo di verificare la conformità dei prodotti acquistati) e nell’expediting (monitoraggio dell’avanzamento e del rispetto dei tempi di consegna). Dopodiché il prodotto è pronto per la spedizione e passa in carico alla logistica, che avrà la responsabilità del trasporto dalla fabbrica dove l’elemento è stato prodotto (in questo caso in Italia), fino alla fondazione, ovvero all’area interna della raffineria di Omsk dove la colonna di trattamento oli andrà montata.
Continua Santi: “Le quattro fasi che abbiamo descritto sono il risultato di un processo che deve svolgersi nel massimo rispetto di tempistiche, modalità, qualità e sicurezza. Per arrivare a questo, l’ingegneria e il procurement - coordinate dagli uffici di Milano e Mosca - hanno lavorato in modo eccellente, addirittura in tempi dimezzati rispetto alla media”.
Una reputazione meritata
La storia di un trasporto dai requisiti eccezionali - e dalla progettazione del tutto originale in funzione delle specifiche particolarità ambientali - è un caso simbolico che ci aiuta a parlare dell’importanza delle singole decisioni, del supporto organizzativo e dell’accountability di ogni componente del team: dagli ingegneri di progetto, il responsabile della sicurezza e fino al tecnico che comanda elettronicamente il mezzo su cui la colonna viene spostata all’interno del cantiere.
“L’ottima reputazione di Maire Tecnimont in Russia non nasce per caso - spiega Rolandelli - ma è frutto di radici storiche che partono da lontano, con decine di impianti realizzati nei settori petrolchimici, trattamento gas e fertilizzanti. Negli anni ’70 la Russia voleva rendere le città più importanti dell’Unione Sovietica energeticamente autosufficienti, dotandole di raffinerie, impianti chimici e centrali nucleari. Durante il periodo della Perestroika tra la fine degli anni ’80 e l’inizio degli anni ’90, ricordo che a Mosca Tecnimont stava costruendo ‘chiavi in mano’ un impianto per trasformare il propilene in polipropilene. Nonostante il periodo fosse estremamente difficile sotto il profilo della sicurezza personale, siamo tutti rimasti ai nostri posti, completando il progetto. A quell’epoca il trasporto dei materiali era molto complesso, ma noi riuscimmo a organizzare uno spostamento fluviale di elementi lunghi 80 metri sulle acque della Moscòva che passa davanti al Cremlino. Questo episodio, insieme ad altre decine di esempi, costituiscono le nostre credenziali per continuare a operare in Russia ai massimi livelli”.