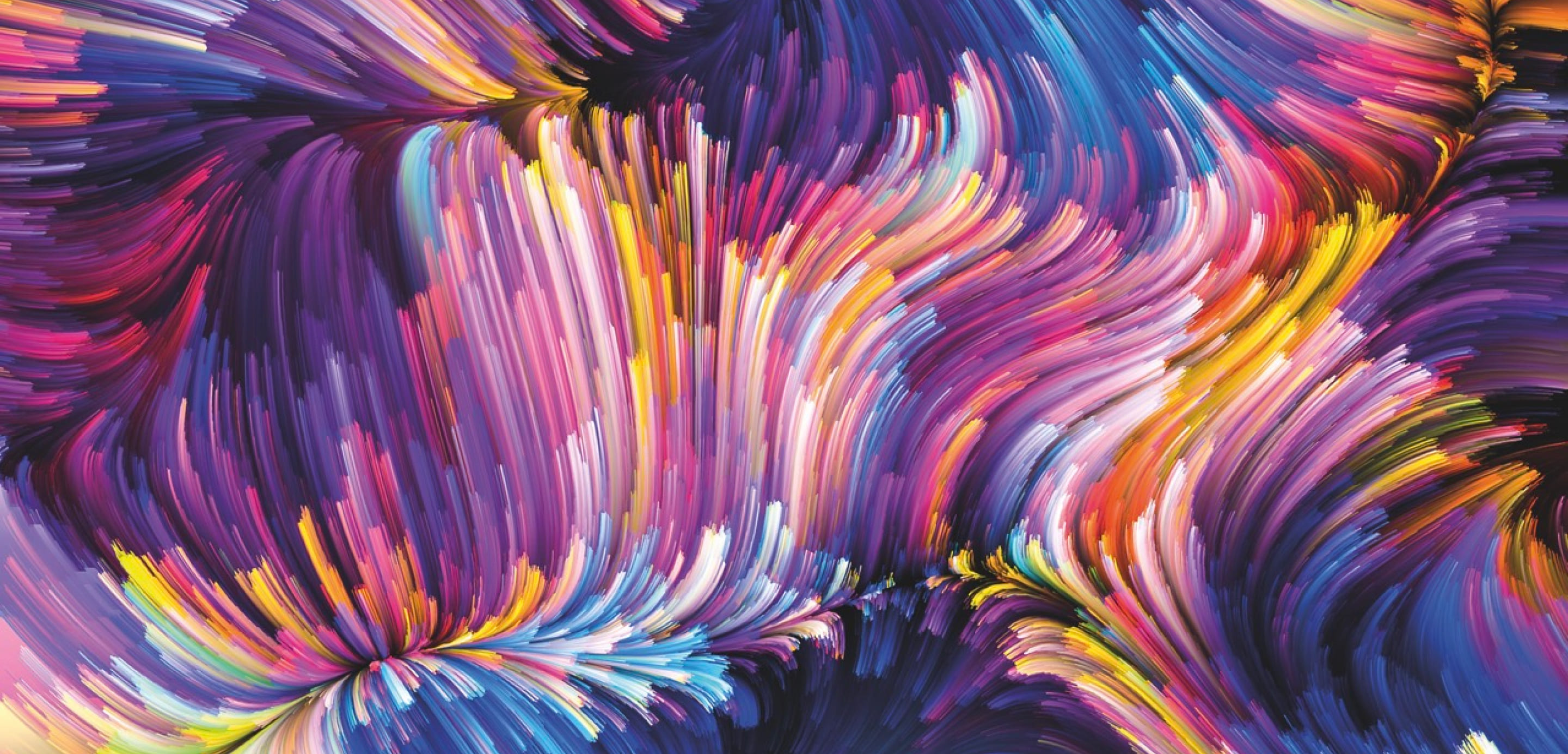
Along the path to get out of the Covid-19 emergency and relaunch the economy, the strategies that look toward the sustainable goals of the United Nations shift the focus from a linear economy to a circular one, based on a system designed to reuse materials in subsequent production cycles, reducing waste and the supply of virgin raw materials to an absolute minimum. «By implementing the mechanical recycling of plastics, and promoting the chemical one at the same time, we are able to shape an economy designed for self-regeneration - explains Fabrizio Di Amato, Chairman of Maire Tecnimont. This is in essence an existential transformation». According to the report of the World Bank “What a Waste 2.0”, every year we generate about two billion tons of waste. «If we don’t take urgent action - says Di Amato - by 2050, with the increase in global population and urbanization, global waste will increase by 70%, with a production of 3.4 billion tons».
Waste is the new oil, although for decades the cost to dispose of it has been high, both in economic and environmental terms. Now with the new project of the Circular Districts, thanks to its proprietary technologies, NextChem - a Maire Tecnimont group company that was conceived from the concept of energy transition, circular economy and green chemistry - is able to produce new products and raw materials for industry from waste, contributing to the reduction of emissions. Di Amato explains: «During the States-General of Economy held last June, convened by the Italian Prime Minister Giuseppe Conte, we presented NextChem’s Circular District model, which represents a solution for both reducing the amount of waste disposal as well as for the green conversion of industrial sites in the petrochemical and steel industry, traditionally based on resources and raw materials of fossil origin».
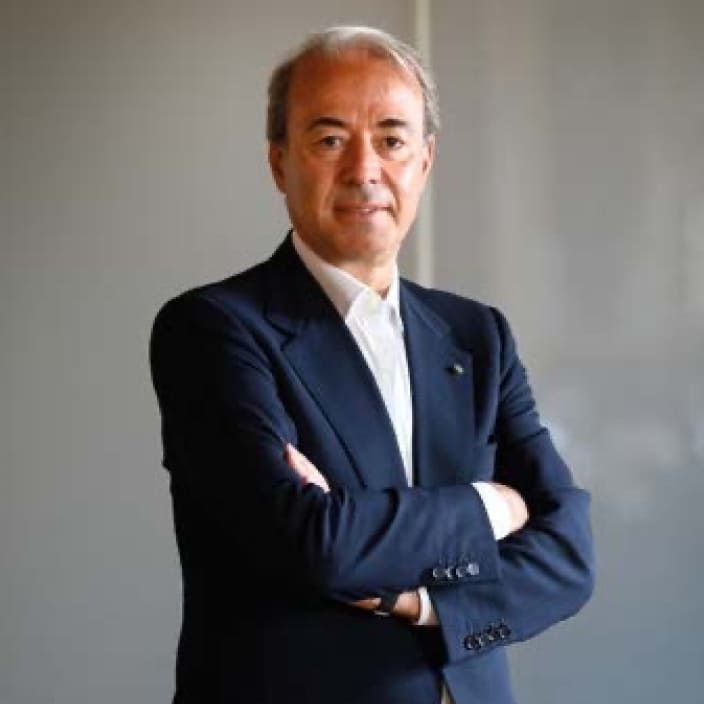
«Waste is the new oil» explains Fabrizio Di Amato, Chairman of Maire Tecnimont. «By implementing mechanical recycling of plastics and promoting chemical recycling, we are shaping an economy designed to regenerate itself». Simultaneously helping the reconversion of industrial sites in the petrochemical and steel industries.
The model integrates technologies allowing for a quality mechanical recycling of plastic waste and for the chemical recycling of plasmix and RDF through a chemical conversion process that makes it possible to obtain synthesis gas from which compounds such as hydrogen, methanol and ethanol are produced, the latter which at the moment is completely imported from abroad in our country. In addition, the district can also integrate green hydrogen production technologies through electrolysis from renewable resources.
«With the Circular Districts - says the Chairman - not only do we significantly increase the recycling rate of our country, but at the same time wereduce the emissions altering climate, promote sustainable mobility, create jobs, professional growth and new opportunities for the territory and the companies in the sector. In addition to meeting the objectives of the National and International (EU) Action Plans on the subject, the solution overturns the concept of waste as a problem to be disposed of, since it replaces the chemistry of coal and oil with a chemistry based on the recovery of resources that would otherwise be discarded. A sustainable solution from an environmental, social and economic standpoint, of which Italy can become a leader in Europe, winning the challenge of change».
The model developed by NextChem
The valorization of consumption waste, the extension of the life cycle of products, the use of secondary raw materials for recycling and the use of energy from renewable resources all contribute to the definition of a model of sustainable development for the environment and economic growth. The model developed by NextChem includes an integrated platform of green chemistry technologies and, more precisely, quality mechanical recycling (Upcycling) of plastic waste, chemical recycling of plastic waste and dry waste and production of green hydrogen through electrolysis.
The patented Upcycling technology makes it possible to obtain perfect circularity, transforming post-consumer plastic waste into high quality polymers (and able to replace virgin plastic). While DownCycling – that is, simple recycling - gives waste a chance to be reused in “poorer” products, Upcycling gives the original characteristics of a virgin material back to the recovered plastic, increasing its environmental and economic value. Di Amato explains: «In Italy we have already implemented this technology in an industrial plant in the province of Brescia. Managed by MyReplast Industries (a subsidiary of NextChem) the Bedizzole plant is currently one of the largest and most advanced in Europe: in one year we have transformed 40 thousand tons of recycled polymers, equal to the plastic consumption of one million people. This activity has made it possible to save 270,000 barrels of oil per year, equivalent to about 8,500 tons of CO2».
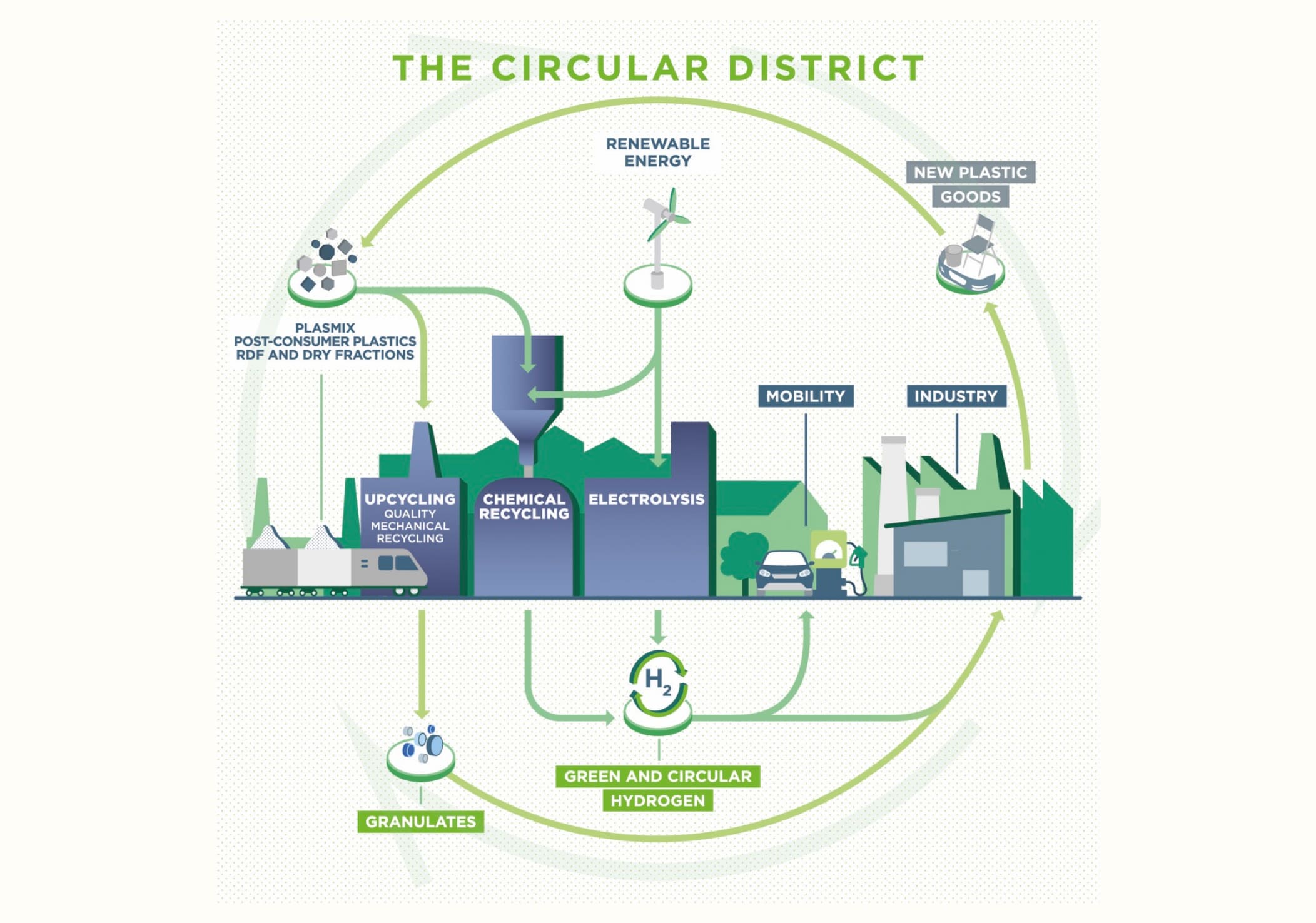
As previously mentioned, the Circular District model is particularly suitable for the green conversion of traditional industrial sites with processes based on the use of raw materials derived from fossil resources, which would be replaced with feedstock derived from renewable and circular resources. «The contribution to the decarbonization and green conversion of brownfield industrial sites - says Di Amato - began with a project in collaboration with ENI for the Venice refinery with the aim of producing Circular Hydrogen. Another project involves the refinery of Livorno, where we will produce methanol again using the same process, while in Taranto the Circular District model designed for the territory foresees the partial replacement of feedstock deriving from fossil resources, currently used by the industries of the industrial sector. The production of Circular Gas will be placed in a context of industrial symbiosis, thanks to an industrial district of excellence in which the infrastructure, facilities and skills of the former Ilva steel plant and the Eni refinery remain».
At the end of September 2020, the Alliance for the Circular Economy comprising 17 companies (including NextChem) presented a position paper for the development of a circular economic model. According to the Alliance, a unique opportunity has arisen today to relaunch a coordinated and decisive commitment to a new development model. «The Covid-19 crisis - explain the companies - reinforced what the climate crisis predicted and showed how systems (natural, economic and social) are strongly interconnected: pursuing a circular economic model is not only an obligation but an opportunity to relaunch the overall competitiveness of the country». The vision of the Alliance calls for a circular development that starts from the enhancement of Italian excellence, and which will be realized, on the one hand through the support of companies to promote sustainable innovation, and on the other hand through the involvement and support of the supply chains, in order to extend the useful life of products and maintain their value. «Networking with the companies of the Alliance for the Circular Economy - concluded Di Amato - allows us to compare these issues from a broader perspective. The aim is to provide a stimulus for these issues to grow in the economic world and in civil society».
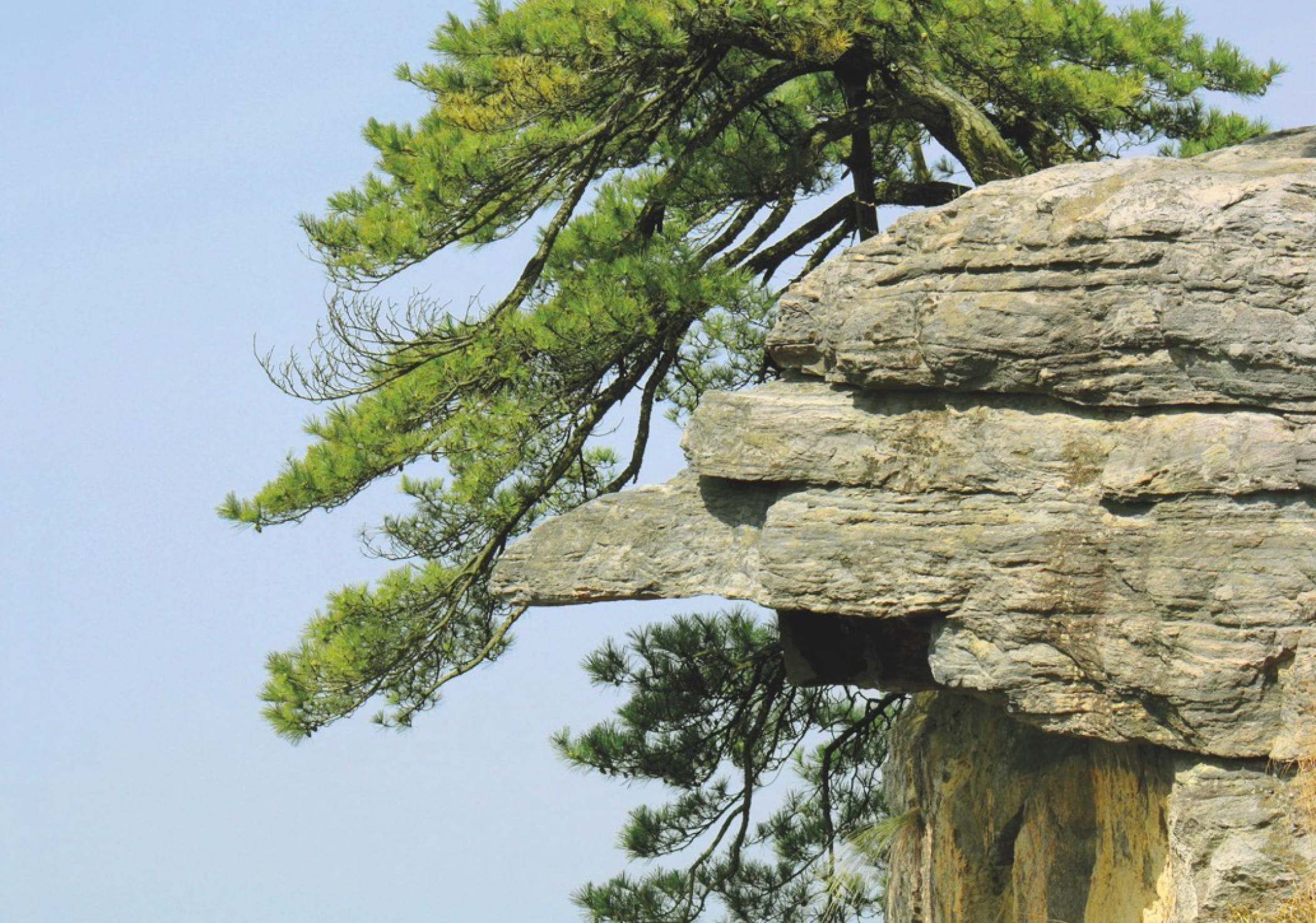
THE TECHNOLOGICAL SOLUTION DEVELOPED BY NEXTCHEM, INTEGRATING SEVERAL ESTABLISHED TECHNOLOGIES, COMBINES TWO OBJECTIVES, CIRCULAR ECONOMY AND DECARBONISATION.
CHEMICAL RECYCLING
The technological solution developed by NextChem, integrating several established technologies, combines two objectives, circular economy and decarbonisation. On one side it provides for the domestic production of chemicals that are currently imported from abroad. On another side, it allows the green relaunch of brownfield industrial sites, with positive consequences for the sector industries and employment.
A central element of the technology platform is the chemical conversion of hydrogen and carbon contained in Plasmix (the waste discarded from sorted plastics) and RDF (Refuse Derived Fuel consisting of plastics and other dry material separated from organic matter) into a valuable chemical product, synthesis gas. This gas is obtained through a process of partial oxidation, followed by a subsequent purification phase, which does not produce pollutants: for this reason, it can be considered a “Circular Gas”, as it comes from post-consumer materials that are recovered in this way.
Circular Gas can be used as it is, due to its reductive qualities, in production processes such as steelmaking and as a replacement for synthesis gas produced from methane or coal derivatives (such as carbon dust), reducing the emissions altering climate generated and with a lower cost. Circular Gas can also be used as a base for the production of “circular hydrogen”, or methanol, or ethanol, or a variety of other chemical compounds essential for industry. These “circular” chemicals reduce the need to extract fossil fuels, reducing imports, contributing to decarbonization and recycling, and providing low-carbon fuels to the transport sector, a sector that has a significant impact on global CO2 emissions.
As part of the “Waste to Chemicals” technology, conversion plants are currently being designed in Italy, one for the production of circular hydrogen for the Eni refinery in Venice and one for the production of circular methanol for the Eni refinery in Livorno. A plant for the production of synthesis gas and circular hydrogen at the Eni refinery in Taranto is also currently under study.
Towards environmental resilience