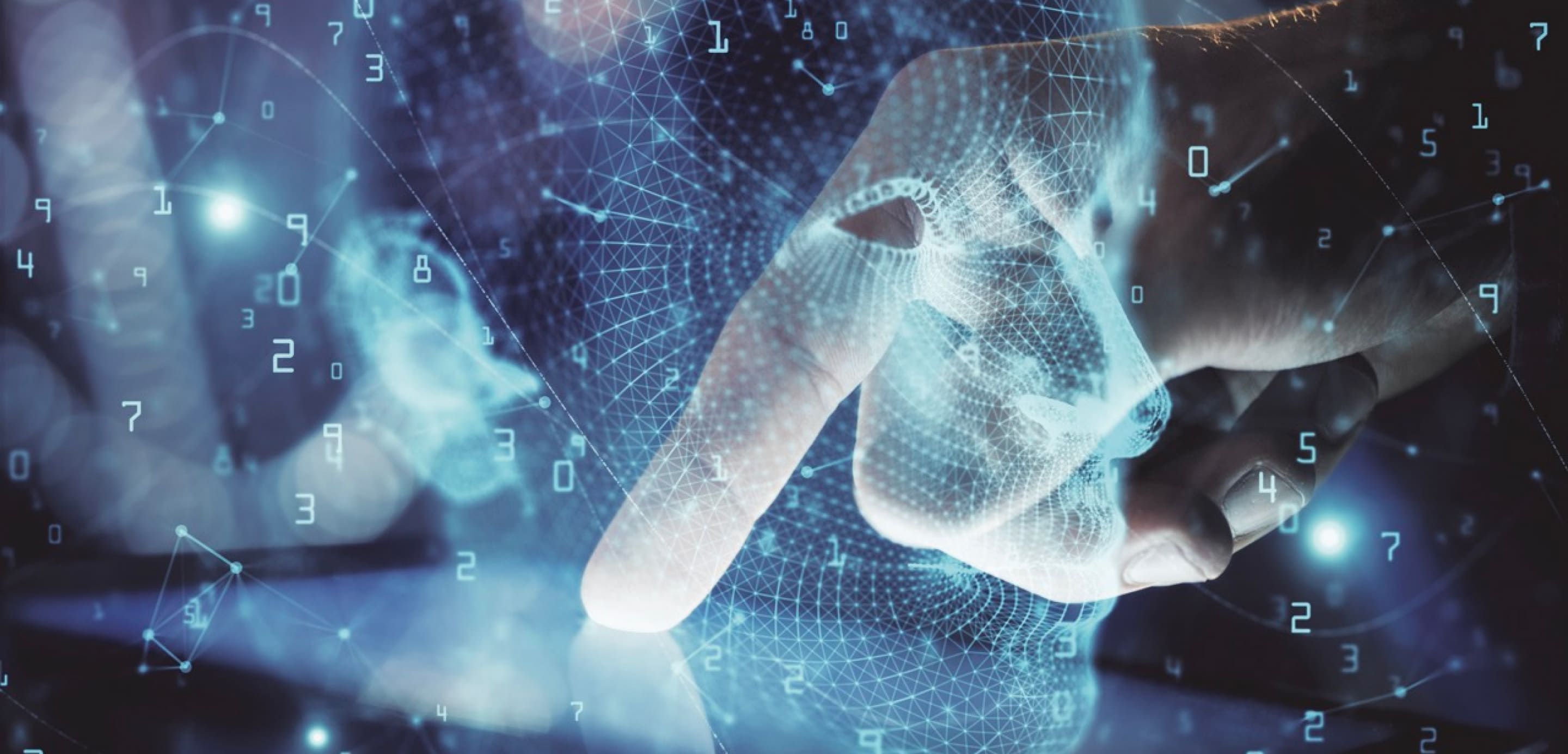
How does digital transformation contribute to the green transition? Here’s how Maire Tecnimont designs and builds more efficient and resilient industrial plants by decarbonizing the entire value chain.
How do we envision the plants of the future? They will be “natively digital” industrial plants, more adaptable and sustainable in terms of total cost of ownership and environmental impact. Plants that are not only more efficient, but also much more profitable and with a smaller carbon footprint.
The international scenarios that the main EPC Contractors operate in are going through a phase of great transformation, especially due to the change of pace required by the “ecological transition” combined with the availability of technology offered by the “digital transformation”. The increasing complexity of plants, the way EPC projects are carried out, and the increasingly challenging contractual requirements are forcing companies all over the world to adapt to new market conditions and to raise the level of competitiveness through targeted strategies, including those based on digital leverage.
To talk about future-proofing industrial plants in the era of digitalization and decarbonization, and to understand how Maire Tecnimont, in the arena of the energy transition, has “embraced” the ongoing change, leveraging its many years of experience as an EPC contractor in highly complex projects, we have gathered an appropriate group of managers within the Maire Tecnimont Group, Max Panaro (Group Organization, ICT and System Quality Vice President), Ezio Pasqualon (Digital Transformation Services Head of Department), Guido Tornatore (Digital Portfolio Management Head of Department) and Michele Mariella (Group Chief Information Officer). We discussed with them how the energy transition is prompting companies to rethink their business models, particularly in the sectors of hydrocarbon processing and green chemistry.
«We all know that the world is aiming for carbon neutrality by the middle of this century, – explains Panaro – so new industrial plants, which will last 20-30 years, must be designed to minimize their carbon footprint throughout their entire life cycle (from plant design to decommissioning). A top priority for plant owners is to adapt to this new business environment, minimizing the “total cost of ownership” for new industrial plants by making a far-sighted investment in digital technology. Digitalization is, in fact, the only lever that plant owners have to ensure flexibility and adaptability, and thus meet energy transition goals with an industrializable approach. The proper use of digital leverage will make it possible to achieve the ambitious goals set by the market, enabling the cutting of plant operating costs (OPEX) by around 30% within 2030 and, above all, reducing their energy consumption».
Although the market has high expectations for digital technology, a good portion of digital initiatives fail to achieve their goals. In the query for solutions, the Group’s pioneering Digital Transformation team has worked extensively to identify key success factors toward digitalization. «We believe that technology should fit the plant owner’s business model, not the other way around» Pasqualon explains. «As an important step toward more effective project execution, at Maire Tecnimont we have used digital technologies to transform and simplify internal EPC processes: this gives project management teams full control over data involving the status of all EPC activities» explains Tornatore. «The company – Mariella explains – is eliminating inefficiencies in its workflow through a comprehensive digitalization program that makes data simultaneously available across the entire stakeholder chain, reducing cost overruns and dramatically reducing turnaround time».
The goal is to become competitive by creating value both during the EPC phase and in the plant operation phase. Therefore, with the digital solutions and services of the NextPlant platform, Maire Tecnimont guarantees the realization of fully digital plants, from the design phase to the operation phase, maintenance included. Panaro adds: «This internal digitalization of work processes is the enabler of a digital portfolio called “NextPlant”. The concept aims to design and build industrial plants that are more efficient, resilient and profitable and much less energy intensive». «Since the goals of decarbonization and reduced operating expenses must be considered in synergy, – Pasqualon explains – NextPlant is designed to make it easier to achieve energy transition requirements by decarbonizing processes and operations across the entire value chain».
This focus on cutting plant operating costs must be embraced by developers from the first phase of a project (or front-end engineering design) to pave the way for a new generation of plants: «true adaptive platforms in the place of traditional static complexes designed and built in the past decades» explains Pasqualon. In fact, carbon reduction targets set by global policymakers require the entire technology supply chain to commit to significant reductions in energy consumption, which is one of the most significant operating costs.
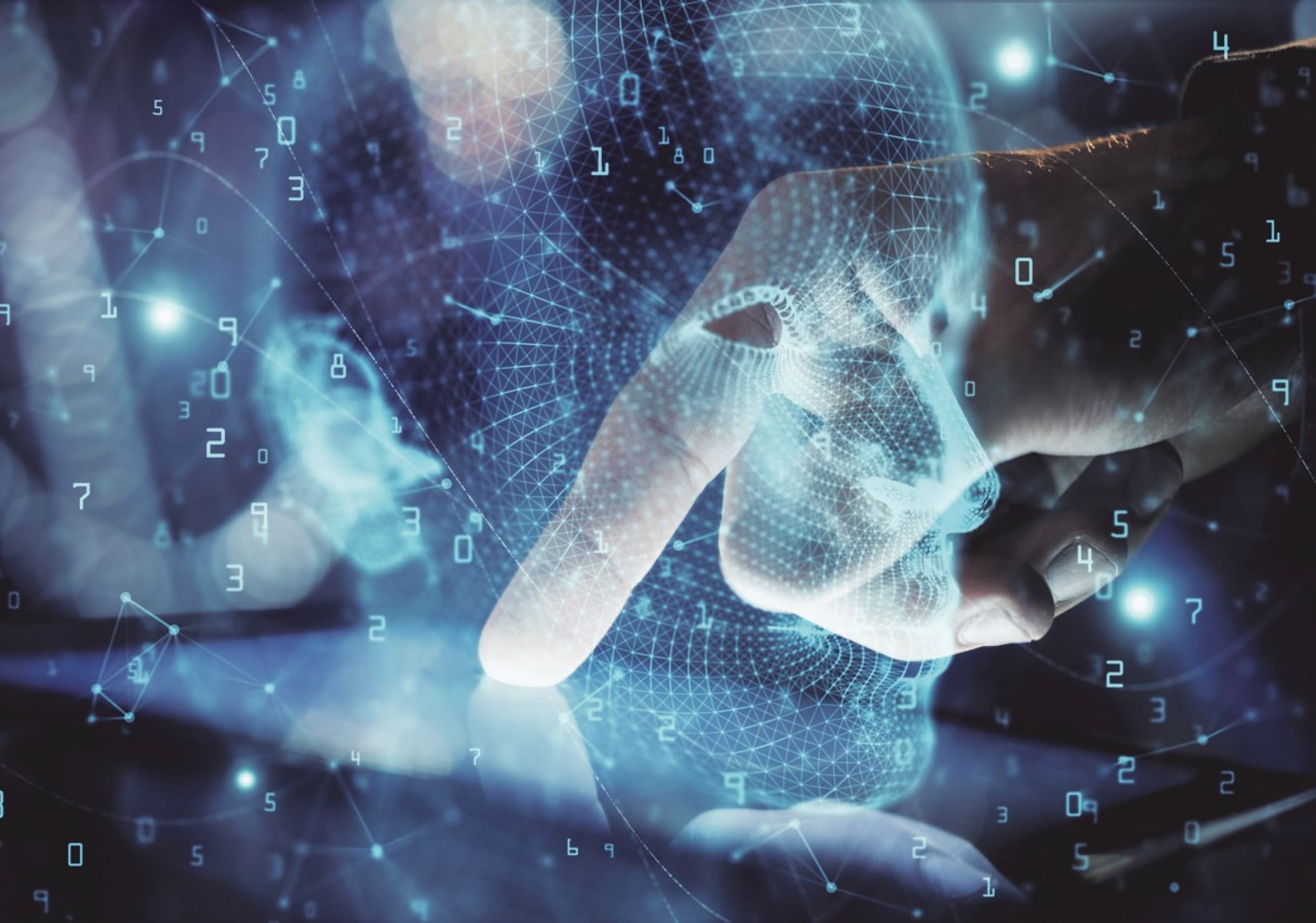
DIGITALIZATION IS, IN FACT, THE ONLY LEVER THAT PLANT OWNERS HAVE TO ENSURE FLEXIBILITY AND ADAPTABILITY, AND THUS MEET ENERGY TRANSITION GOALS WITH AN INDUSTRIALIZABLE APPROACH.
Artificial Intelligence, 5G and Blockchain
When we talk about key technologies to generate value in industrial plants, one of the buzzwords of the future (but also of the present) is undoubtedly “artificial intelligence.” This is not only a powerful driver for the reduction of maintenance costs, but a tool that, by enriching the process models of plants based on conventional thermodynamic and kinetic equations, could eventually result in a reduction of energy consumption by 5-10%, exceeding the approximations of the process modeling existing to date based on first principle models. «Today, artificial intelligence and the enormous availability of data – Pasqualon explains – make it possible to create a “digital twin” of the plant, which allows energy consumption and the various phases of the chemical process to be optimized in real time. The contractor of the future becomes a sort of “orchestrator” of the value chain, an independent technologist able to “hybridize” different worlds».
With future wireless and hyper-connected plants increasingly based on 5G technology, contractors will be able to reduce the use of cables, cable trays and support racks, as well as potentially decrease the plant footprint. All of this will also allow different generations of operators to coexist operationally: think of the process engineer working in synergy with the data scientist, or the large corporation that must develop technologies together with start-ups by leveraging the open innovation approach.
«By using the Internet of Things (IoT) technology and the application of virtual reality – Panaro says – we will increase the productivity of field operators and reduce the risk of errors. Thinking about NextChem, future green chemistry plants geared toward energy transition goals will be smaller, easier to operate and more widely “distributed” via a collaborative network». «This is where the issue of cybersecurity comes in – Mariella points out – as a design criterion and not as a problem to be addressed after a cyber-attack, when it becomes costly and difficult to solve. The only way to be effective is to tackle cybersecurity with a holistic approach: adopting the expression “cybersecurity by design” that involves the entire supply chain».
The discontinuity required by the energy transition also involves the adoption of digital technologies that are not fully mature as of yet, such as Blockchain. As Pasqualon explains, in Maire Tecnimont’s vision, Blockchain – which enables the management of critical information, guaranteeing its transparency, integrity and inalterability – can be used to certify the carbon footprint of the raw material used both in green chemistry processes and in the transformation of conventional hydrocarbons. This step not only guarantees access to possible green awards, but also demonstrates its contribution to decarbonization. The same technology can be used to certify the environmental footprint of the product that has been processed, demonstrating its sustainability and thus obtaining additional incentives.
An approach of Open Innovation
Digital transformation, therefore, plays an important role in all issues concerning sustainability. On the one hand, it dematerializes the physical conception of the workplace in favor of remote work; on the other, it makes information and data fully transparent and accessible, eliminating role, generational and gender gaps. How then can we imagine a “digitally sustainable” future? How will technologies have to develop to contribute to the creation of a better world, considering their role and the effect they have on the environment, economy and society? «It is fundamental – says Pasqualon – for transformations to be developed considering sustainability itself as an “intermediate objective”, and not as an end in itself. To ensure that the virtuous mechanism is set in motion, however, a concerted effort by entrepreneurs, companies and society at large is required. With the aim of understanding and explaining the multiple effects of digital systems, and anticipating far-reaching structural changes from a standpoint of sustainability».
It is useful, then, – as Maire Tecnimont has done – to adopt an “open innovation” approach, embracing external cooperation and rejecting the “silo” mentality of non-adaptive organizations. «Our digital transformation – Panaro explains – is intertwined with the strategies of sustainability. Three-quarters of our digital solutions support transparency and inclusion. 70% of these solutions support HSE best practices and CO2 reduction. Twenty-five percent support knowledge and skills transfer in the countries where we operate. The new vision will be increasingly based on sustainability as a competitive lever and enabling factor, capable of fostering business opportunities and innovative development». The business of the future? «It will be done – concludes Pasqualon – by combining technological innovation, sustainability, social responsibility, inclusion and green chemistry through the use of digital leverage as an enabler of change».
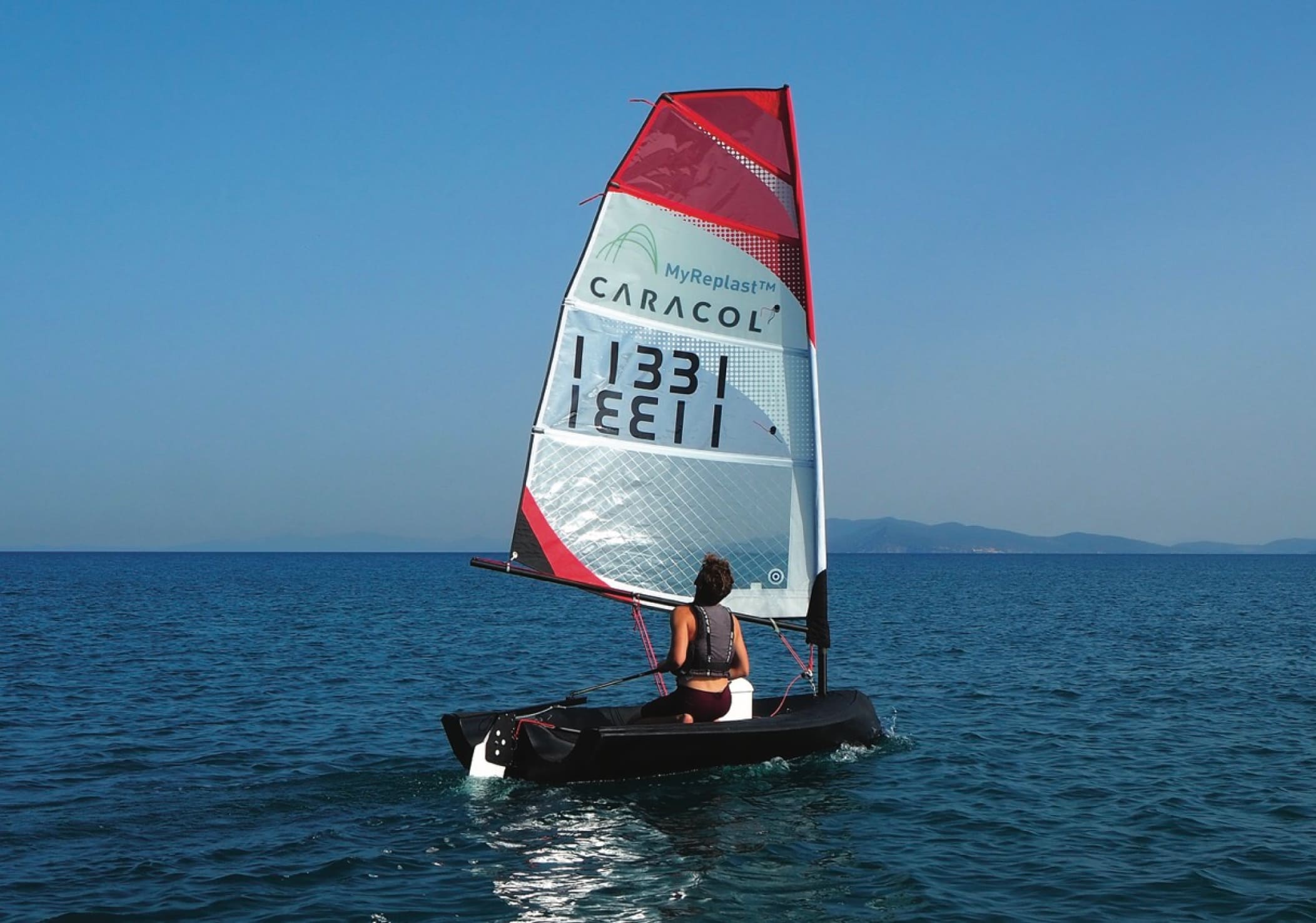
IN 2021, WITH MYREPLAST RECYCLED MATERIAL, CARACOL AND NEXTCHEM CREATED “BELUGA”, THE WORLD’S FIRST 3-D PRINTED SINGLE-HULL SAILING BOAT PROTOTYPE. AN EXAMPLE OF COOPERATION BETWEEN ADDITIVE MANUFACTURING, RECYCLING AND PLASTIC UPCYCLING...
Knowing that the transformation of waste is the real sustainable challenge of the future, Maire Tecnimont is committed to the growth of the circular economy by looking at the system from a broader perspective, capable of grasping the symbiosis among different sectors, between agriculture and industry, between the agro-food chain and chemistry: what for one is waste, for the other can become raw material. Hence the importance, for example, of our proprietary Upcycling technologies, which enable perfect circularity by transforming post-consumer plastic waste into high-performance polymers that can replace virgin plastics. Or of our bio-based green chemistry technologies, which enable integration with existing plants to produce intermediates and biofuels from residual oils and fats. As well as chemical recycling technologies that facilitate the production of circular gas, circular hydrogen, alcohols and hydrocarbons, plus other valuable molecules from non-recyclable plastic and dry waste. With a double benefit on the circularity and CO2 reduction front, without neglecting sustainability on an economic level.
Among the Blue Oceans - places where we can assert our initiative in innovation and our ability to anticipate demand - is the choice of Chairman Fabrizio Di Amato to finance the Chair of Open Innovation and Sustainability at Luiss Guido Carli in Rome, entrusted to Professor Henry Chesbrough, intellectual father of the very concept of Open Innovation and director of the Garwood Centre for Corporate Innovation at the University of California at Berkeley. It is a course of study for managers, entrepreneurs and professionals who will have to handle continuous innovation as an evolutionary process according to an open-minded approach: a step into the future that helps companies, large and small, transform from closed to open organizations. Since, to quote Chesbrough himself, «there is “raw material” out there of such high quality that even the brightest companies can’t afford to sit back and ignore it».
The “revolutionary” table