- Röhm will supply the PMMA scrap material to be processed by MyRemono via the NXRe™ PMMA technology and chemically transformed into ultra-pure monomers with virgin-like quality against a tolling fee
- MyRemono’s investment for the technology development and scale-up, as well as for the construction of the first industrial-scale plant, is currently expected to be approximately €15 million, mainly funded by a bank loan and the EU Innovation Fund grant
- The facility, expected to be completed by 2026 in Italy, will yield recycled MMA with GHG emissions reduced by over 90% and process 5,000 tons of PMMA per annum, sufficient to produce about 10 million car taillights
- The agreement follows the establishment of a Europe-wide circularity network for PMMA, including MyRemono, Röhm, Pekutherm and Polyvantis
Milan, 16 December 2024 – MAIRE (MAIRE.MI) announces that NEXTCHEM (Sustainable Technology Solutions), through its subsidiary MyRemono, has signed a Toll Manufacturing Agreement with Röhm under which Röhm will supply PMMA scrap material feedstock to be processed and chemically transformed by MyRemono into ultra-pure monomers with virgin-like quality.
This initiative leverages on NEXTCHEM's proprietary NXRe™ technology, an advanced and efficient molten metal depolymerization process for the continuous chemical recycling of PMMA. Röhm will also act as the off taker of recycled Methyl Methacrylate monomer (rMMA), to be reused for the manufacturing of new PMMA products in a fully circular process. The agreement provides for a processing fee to be paid by Röhm to MyRemono.
The initiative follows the establishment of a Europe-wide circularity network for the recycling of PMMA, which includes MyRemono, Röhm, Pekutherm and Polyvantis. Pekutherm will manage the logistics and sorting of PMMA materials, while Polyvantis will handle the mechanical recycling.
MyRemono will manage the chemical recycling of PMMA scrap material at its first-of-its-kind industrial-scale plant, currently being developed in Italy, with the support of the EU Innovation Fund. The plant is expected to be completed in 2026 with an initial processing capacity of about 5,000 tons per year of PMMA, an amount needed to produce approximately 10 million car taillights, demonstrating how significant volumes of recycled material can replace virgin resources in manufacturing.
Compared to the current virgin MMA production routes, the recycled MMA produced via NXRe™ PMMA TECHNOLOGY is expected to feature a carbon footprint reduction of more than 90 percent[1]. MyRemono’s overall investment for the technology development and scale-up, as well as for the construction of the first industrial-scale plant, amounts to 15 million, mainly funded by a bank loan and the €4 million EU Innovation Fund grant.
With this agreement NEXTCHEM sets the base for the licensing of its NXRe™ PMMA technology, a key milestone for the future development of chemical depolymerization of other value-added materials, such as polystyrene and polyolefins.
Alessandro Bernini, MAIRE CEO, commented: “Our NXRe™ PMMA technology will play a key role in advancing circularity, serving as one of the core pillars of our value proposition for circular solutions and sustainable materials. The implementation of this world-first advanced recycling plant, and the creation of this industrial consortium are a clear example of the relevance and validity of how disruptive technologies respond to current challenges.”
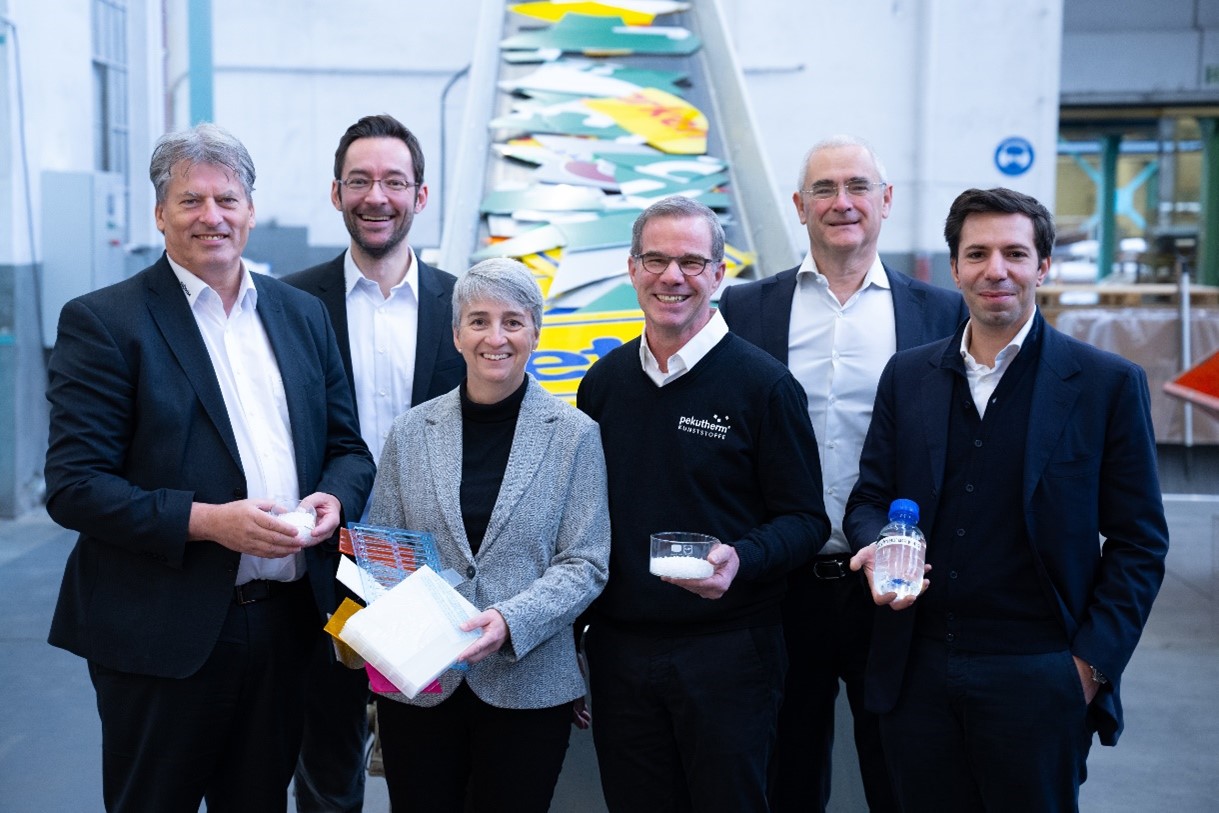
[1] According to the methodology for GHG emission avoidance calculation of the Innovation Fund.
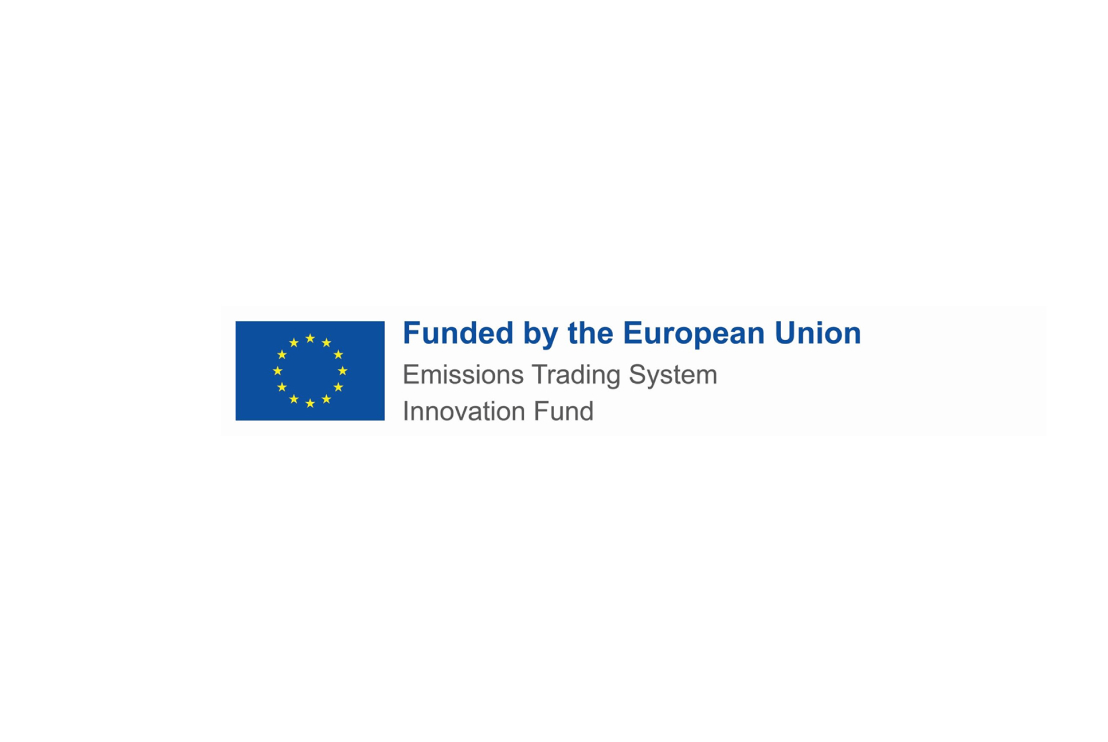
“Funded by the European Union. Views and opinions expressed are however those of the author(s) only and do not necessarily reflect those of the European Union or the European Climate, Infrastructure and Environment Executive Agency (CINEA). Neither the European Union nor the granting authority can be held responsible for them.”